We are Phoenix Laser Solutions, a company dedicated to providing high-quality manufacturing solutions for the power generation industry. This case study highlights our successful application of laser weld repair on impellers. An impeller is used in a centrifugal compressor or pump to increase the pressure and flow of air, gas or liquids.
A customer came to Phoenix Laser in need of weld repairs on their worn impellers. Conventional repair methods like TIG welding introduce excessive heat that can warp the impeller and compromise its functionality within the high-precision environment of a compressor or pump. The customer also required Inconel filler wire, which is traditionally a difficult alloy to weld.
Our expertise lies in utilizing cutting-edge laser welding technology for power generation components. We can precisely weld single critical features without distortion of the surrounding material. Since the heat input is so low, no pre-heat or post weld heat treatment (PWHT) is required.
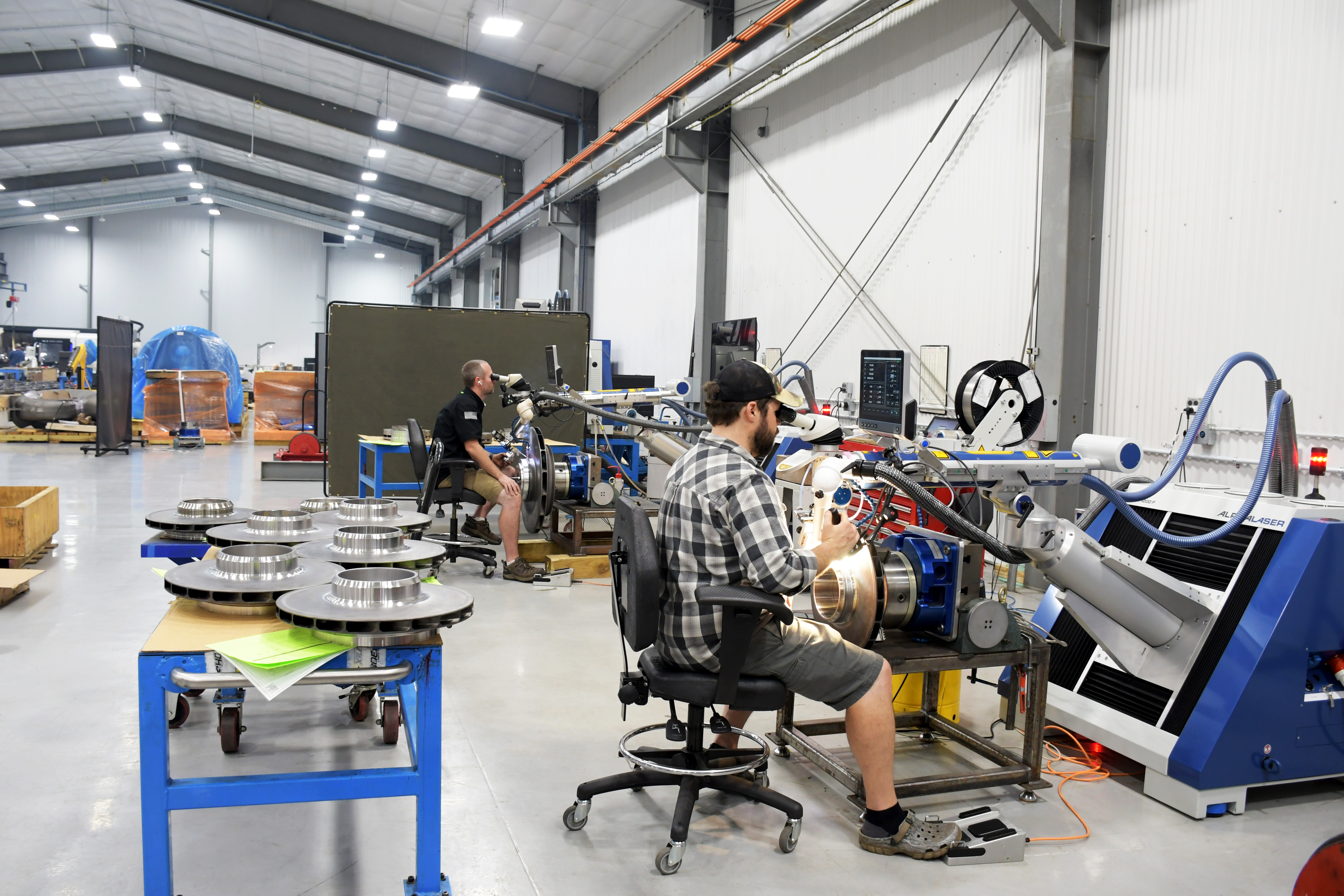
Repair Process:
- Pre-weld Inspection
- Laser Welding (no PWHT required):
- Material: 4340 base material welded with 625 filler metal.
- Filler Rod: 0.025-inch diameter.
- Weld Buildup: 0.040 inches per side on the bore.
- LPI (Liquid Penetrant Inspection): After welding, the weld underwent LPI to ensure there were no cracks or porosity. This non-destructive testing method guarantees the integrity of the repair.
- CMM (Coordinate Measuring Machine) Inspection: The repaired impeller was then inspected using a CMM to verify it met the customer dimensional specifications and would function properly within the compressor.
Advantages:
- Unmatched expertise: Our extensive experience in laser welding for power generation applications translates to exceptional quality and reliable welds.
- Reduced downtime: Due to its precision, laser welding offers a faster turnaround compared to traditional methods, minimizing downtime for customers.
- Minimal heat input: The heat input of laser welding is significantly less than traditional welding. This eliminates the need for pre-heating the impeller before welding and post-weld heat treatment afterwards. In turn, this saves our customers considerable time and money associated with these processes.
- No distortion: Our laser welding process allows for highly targeted repairs. We can weld specific critical features, like seal areas, without introducing distortion to adjacent critical features, such as the bore. This precise control maintains the impeller’s dimensional integrity and functionality.
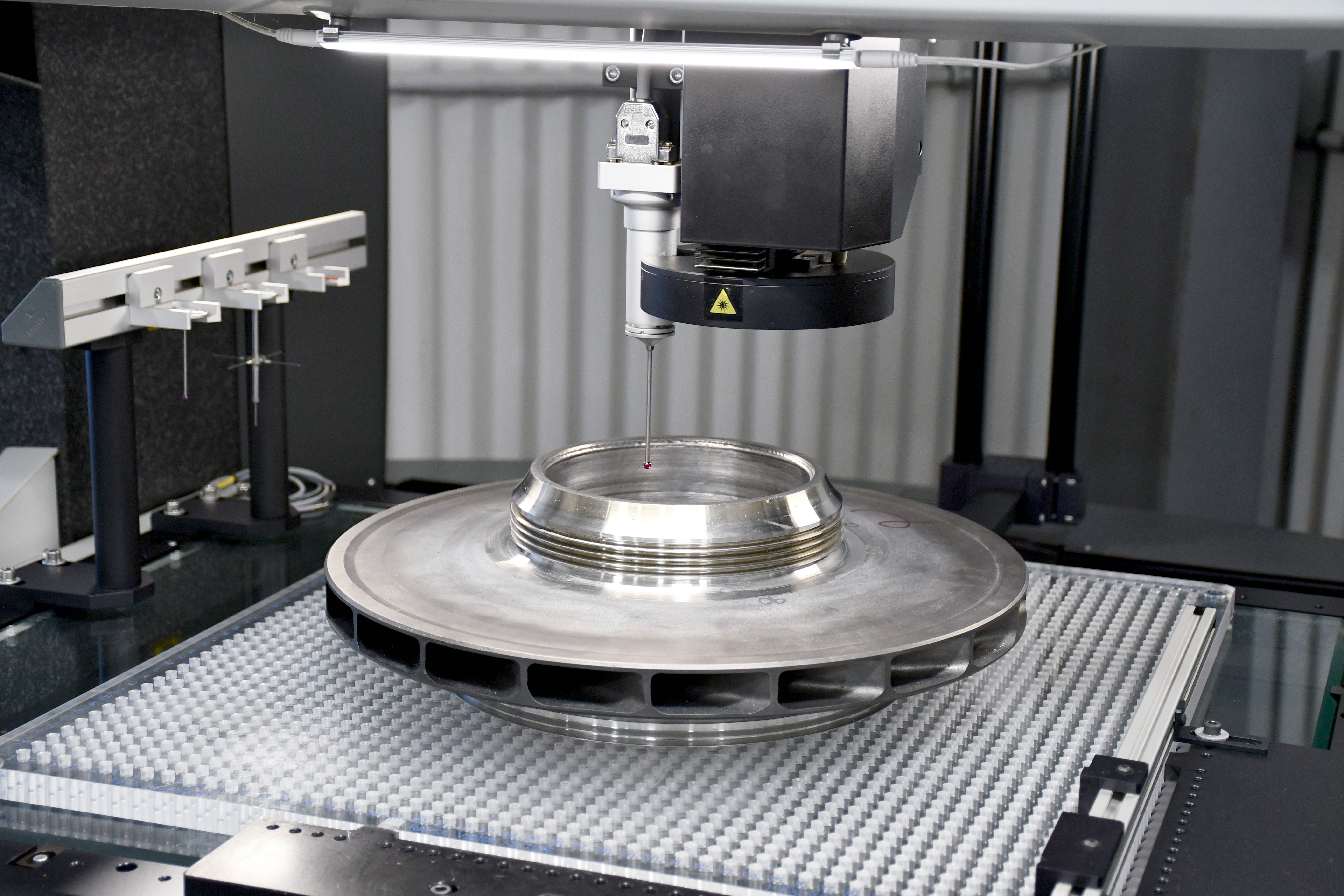
This case study exemplifies the effectiveness of our laser weld repair process for impellers in the power generation industry. Our approach offers significant advantages, minimizing distortion, expediting repair times, and delivering a cost-effective solution while maintaining the critical performance of the components.