We repaired a worn turbine rotor using a powerful 1200 watt fiber laser welder. With a cycle time of 7 hours, we added .015″ of weld to its diameter, ensuring smooth operation and extended lifespan.
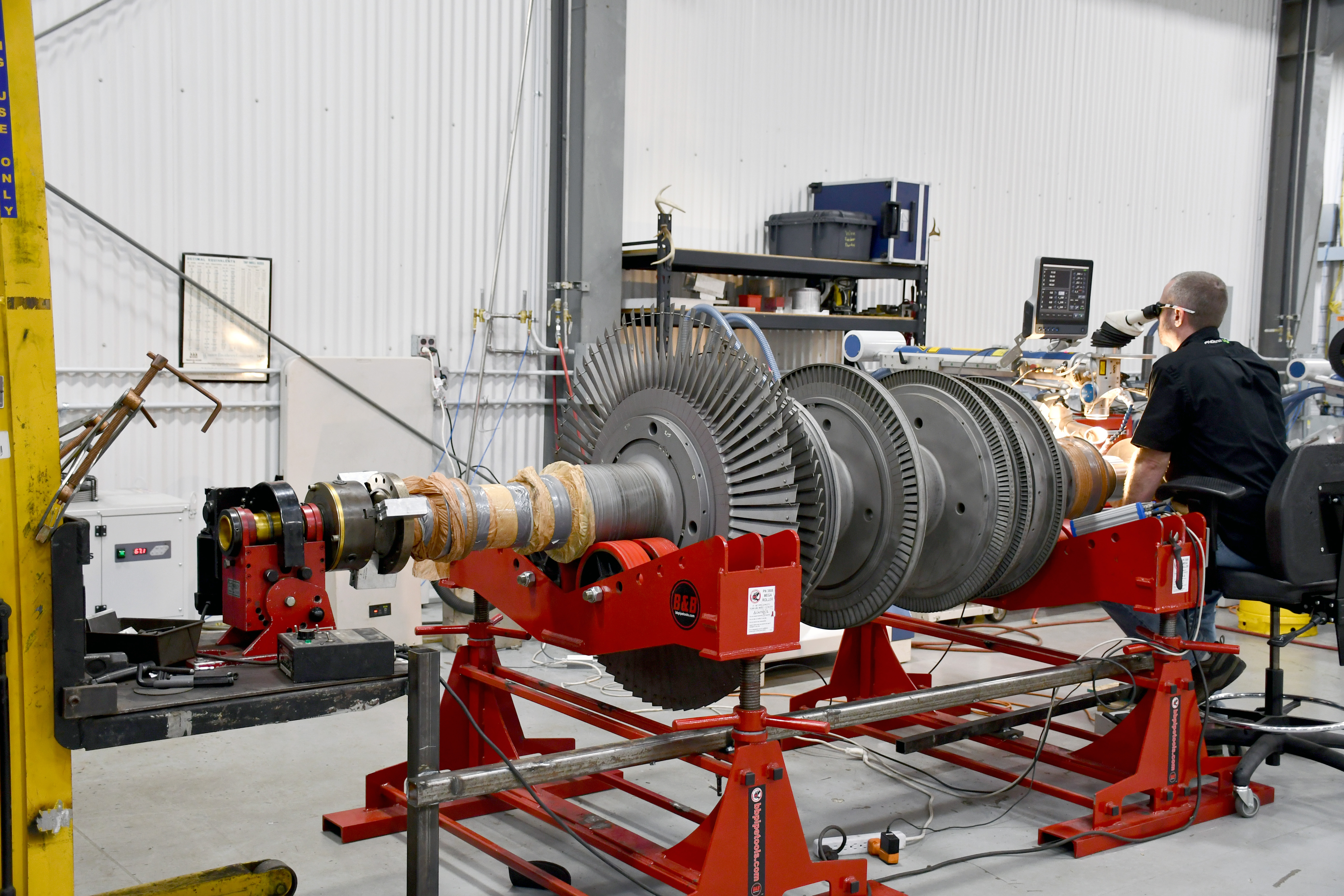
Why was Laser Welding the preferred choice for this repair?
It’s stable, repeatable and precise.
Minimal HAZ
Low heat input eliminated distortion or discoloration.
No extra processes
No pre or post-weld heat treatment needed.
Quick Repair
Repair was made without any disassembly.
Quality Weld Inspection
In-house inspection to ensure welds are to customer specification.